Il Digital Twin con tecnologia ML sta trasformando il settore manifatturiero. E come!
Il settore sta facendo piccoli passi verso l’uso dell’analisi predittiva e dell’apprendimento automatico per promuovere l’efficienza nella manutenzione delle macchine.
L’uso di dati e analisi nell’industria manifatturiera non è stato esplorato al massimo delle sue potenzialità nonostante i progressi in IoT, AI e big data. Una parte enorme del settore fa ancora affidamento sugli esseri umani per la manutenzione delle macchine in officina. Il processo è laborioso e porta a una perdita di produttività e vendite a lungo termine.
Tuttavia, l’industria sta ora compiendo piccoli passi verso l’uso dell’analisi predittiva e dell’apprendimento automatico per promuovere l’efficienza nella manutenzione delle macchine. Arvind Mahishi, AVP e Vighnesh Subramanian, Senior Data Scientist presso Tiger Analytics, hanno parlato dei gemelli digitali basati sul ML al MLDS 2021.
Il gemello digitale è un’alternativa economica, scalabile e autosufficiente per comunicare agli operatori delle macchine le condizioni esatte delle apparecchiature sotto la loro cura. Mahishi ha detto che prende i dati del mondo reale su un oggetto fisico o un sistema come input e prodotti come output per prevedere come l’oggetto fisico o il sistema sarà influenzato da quegli input.
Prima che ML iniziasse a rivoluzionare la manutenzione delle macchine in una configurazione di produzione, i dati venivano raccolti mediante manutenzione reattiva, manutenzione programmata, cronologia degli allarmi e analisi delle cause alla radice; sia dispendioso in termini di tempo che insufficiente. Con AI e ML al centro della scena, la manutenzione predittiva e prescrittiva ha fatto un’enorme differenza nella qualità della raccolta dei dati.
L’industria manifatturiera ora fa affidamento sui dati dei sensori, sui dati di temperatura, sui dati di pressione, sui dati sul flusso d’aria, sui dati meteorologici, ecc. Sulla base di questi dati, stanno producendo processi di stoccaggio e controlli di qualità degli edifici. Il processo di arricchimento dei dati aiuta a identificare le lacune, creare parametri per la gestione dei dati e creare strumenti per accedere alla qualità dei dati acquisiti. I dati sono integrati con gli strumenti BI per creare metadati per la revisione olistica dei dati su ulteriori elaborazioni e analisi dei dati.
Parlando della roadmap del gemello digitale basato su ML, Mahishi ha detto che inizia con un inventario dei dati da apparecchiature e sensori, che aiuta con la valutazione della prontezza dell’infrastruttura complessiva. Altre fasi includono la definizione delle priorità della complessità del valore, PoC e dimostrazione del valore, implementazione e monitoraggio su vasta scala, seguiti dalla misurazione continua del valore del sistema complessivo. In base all’elaborazione dei dati del sensore, viene creato un avviso se la macchina inizia a mostrare irregolarità nei dati raccolti, consentendo all’operatore di eseguire la riparazione preventiva.
Caso d’uso
Mahishi ha spiegato il caso d’uso di una multinazionale indiana produttrice di acciaio per implementare un modello di affidabilità del gemello digitale per migliorare la manutenzione predittiva. Ha detto che hanno dovuto affrontare sfide come dati inadeguati, dati mancanti e pipeline interrotte. Inoltre, i modelli di rilevamento delle anomalie esistenti erano estremamente dispendiosi in termini di tempo, richiedevano la manutenzione del modello individuale e non avevano un quadro standardizzato.
Avvio e rilevamento dei dati: estrarre i dati grezzi dalle apparecchiature seguiti dalla pre-elaborazione e pulizia dei dati
Elaborazione dei dati: implica la regolarizzazione dei timestamp e il ricampionamento all’intervallo di tempo richiesto
Filtro dei dati: rimozione dei dati con bassa varianza
Model data set prep
Rilevamento delle anomalie: ha comportato il test di più framework di modelli, il punteggio dei modelli costruiti sull’intero set di dati
Previsione: identifica le lacune di imputazione nei dati delle serie temporali risultanti dal fatto che l’apprendimento automatico è inattivo / testato. Sono stati utilizzati strumenti come ARIMA, random forest, ARIMAX, Smoothing
L’output finale che riflette lo stato di salute del sistema viene aggiornato su un dashboard in tempo reale. Mostra inoltre i risultati su comportamenti anomali, previsioni di affidabilità e analisi delle cause alla radice basate su sensori. Il monitoraggio dell’interfaccia utente è fondamentale per gli imprenditori per visualizzare lo stato di salute generale nell’intervallo di tempo selezionato.
Evidenziando il risultato aziendale del processo, Mahishi ha condiviso che la loro soluzione ha finora consentito un risparmio di 2,75 milioni di dollari in termini di costi di manutenzione risparmiati e perdite di produzione evitate. Attualmente, i modelli scalabili vengono implementati in altiforni, frantoi, ventilatori, trasformatori e apparecchiature simili.
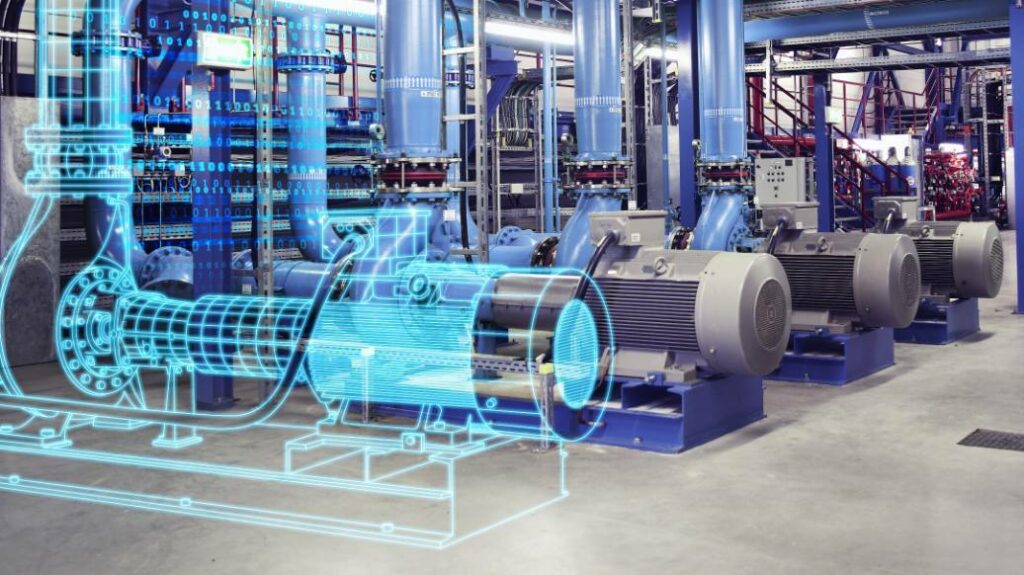